Managing Construction Engineering Projects
Have you ever wondered how large, complex engineering projects manage to monitor budgets, oversee progress, or stay on schedule? Construction sites often run on tight deadlines and narrow budgets, so it’s important that project managers have the right tools to keep everything on track.
Introducing Earned Value Management (EVM) and Earned Value Analysis (EVA).
If you’re not familiar with these terms then fear not - we’ve covered everything you need to know and even put together a free downloadable template for you to get started.
What is Earned Value Management?
Earned Value Management (EVM) was first established by the US Department of Defence in the 1960s and has since been widely adopted by project managers in different industries across the globe. In short, it’s a model of analysis that allows you to track the progress of a project in comparison to the initially predicted schedule and/or budget.
As you can imagine, this is particularly useful for planning and managing large, intricate construction projects. With so many moving parts, materials, tasks, and operatives to keep track of, project managers need to be able to track progress against planned budgets and schedules.
Benefits of using Earned Value Management
Effectively carrying out earned value management will answer three crucial questions about the progress of any construction project.
Where should we be at this point in time?
Where are we at this point in time?
Where will we be if we carry on this way?
Being able to answer these questions confidently (and with data) will enable you to keep senior management and other stakeholders well informed on the progress of the project. More importantly, knowing this information helps manage potential risks and avoid deviating from initial plans and budgets.
Before construction begins, the project manager will agree on the scope of the work that needs to be completed and create a work breakdown structure (WBS).
Each package (group of tasks) within the WBS will be allotted a specific budget and time frame for completion. This plan is then used as a baseline (referred to as Planned Value or PV) which, in turn, is used to monitor progress throughout the completion of the project.
Initial budgets and time frames are built from industry averages and experience from previous projects. It is essential that these are as accurate as possible as deviations can determine whether or not the overall project is profitable.
As work is carried out on each package, the completed tasks become Earned Value (EV) and are used to calculate progress in comparison to the baseline budget and schedule. Delays and deviations from the initial plan can then be addressed, corrected, and planned for.
How to calculate Earned Value Analysis
Now that you understand what EVM is and how it’s used, you’ll probably be itching to find out how it’s done. Fortunately, the theory behind the analysis is fairly simple and you’ll just need the following metrics to get started.
BAC (Budget at Completion)
The original budget assigned to complete the package or task.
AC (Actual Cost)
The exact amount that has been spent to date.
EV (Earned Value)
How much the task should have cost so far
Calculated as:
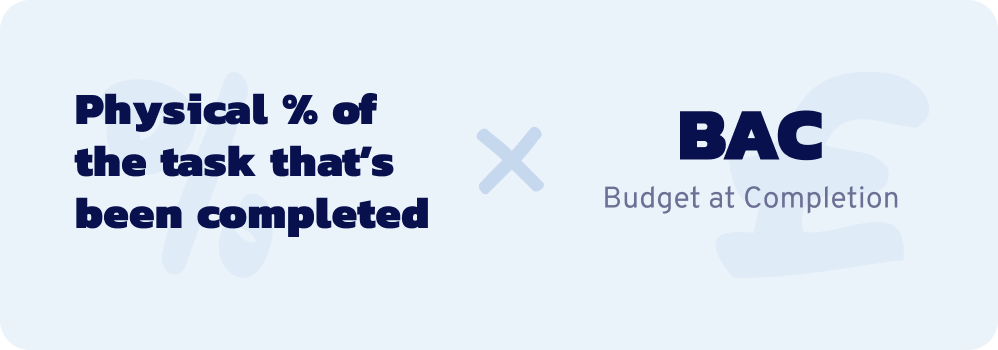
To simplify:
A budget of £2000 has been estimated for the installation of 10,000 bricks
To date, 4000 bricks have been installed (40% of the overall task
The EV is then 40% (percentage of the task complete) x £2000 (BAC)
EV = £800.00
What next?
Using the above formula you should now have an idea of how far along the project is, how much you’ve spent, and how much you theoretically should have spent to date.
The great thing about EVM is that you can add another level of detail by mapping this information out on a chart and comparing your EV against the PV at specific points in time. This is usually carried out at regular (often monthly) intervals so that potential issues and deviations can be managed as soon as possible.
Enjoying this article? You'll love The Ultimate Guide To Construction Reporting.
Calculating Variance
If you want to delve even deeper into variances and deviations, you can use the following formulas to calculate schedule variance and cost variance.
Schedule Variance = EV - PV
Cost Variance = EV - AC
When working on schedule and cost variance it’s important to remember that positive values indicate being ahead of schedule or under budget; negative values indicate that the project is behind schedule or over budget. Anything with a value of 0 is on schedule or budget.
Measuring Project Efficiency
Schedule Performance Index (SPI) and Cost Performance Index (CPI) can be used to calculate project efficiency by assigning a numeric value.
To calculate each you’ll need the same metrics used to calculate variance.
The formulas:
Schedule Performance Index = EV/PV
Cost Performance Index = EV/AC
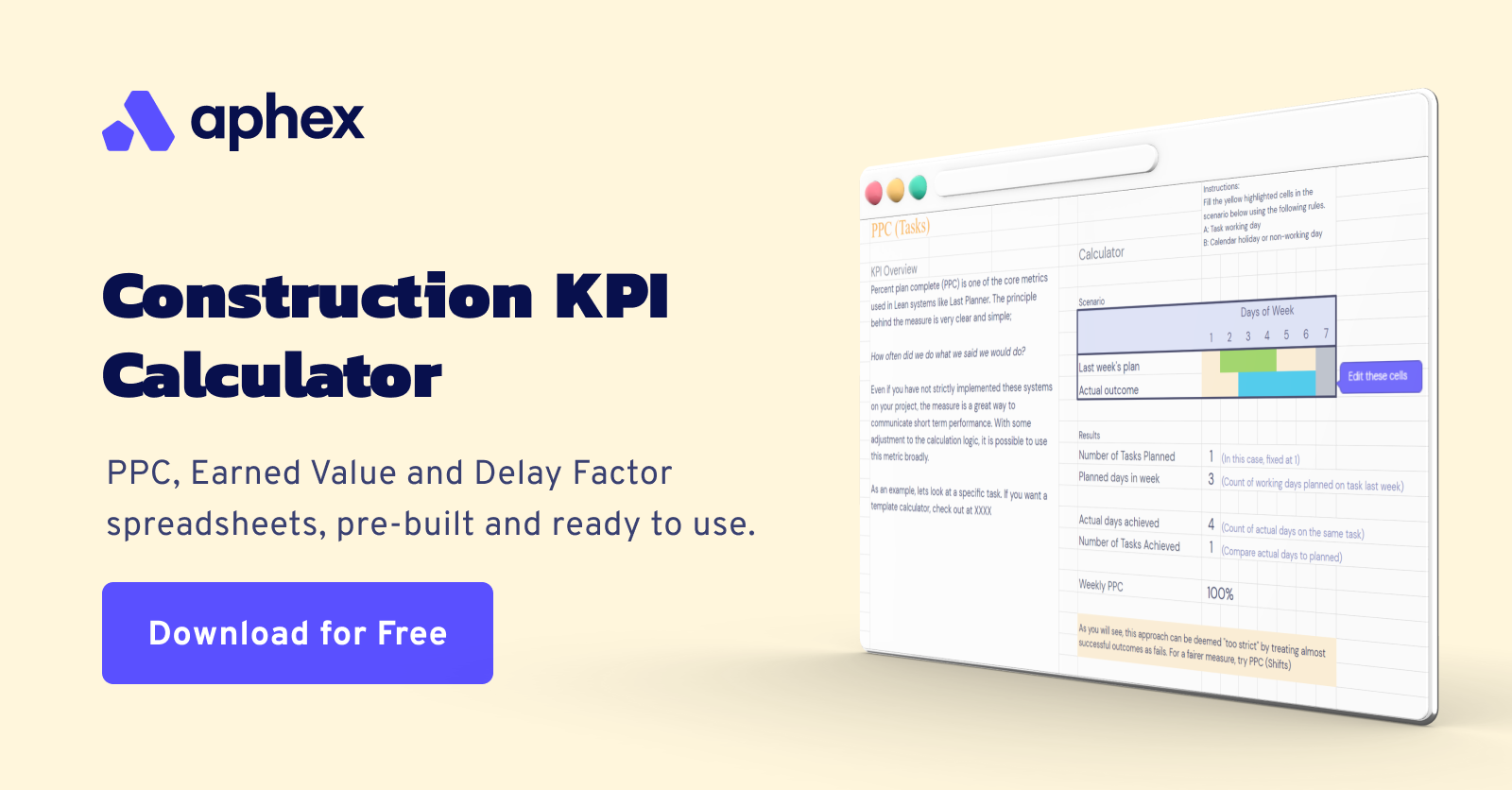
Thanks for reading! If you enjoyed this article and would like to learn more about driving short term performance in construction, check out The Ultimate Guide To Construction Reporting.