The construction KPIs you should be using
Short to mid-term reporting can seem a little hectic sometimes. With every project doing things a different way and so many potential metrics to track, it’s hard to know what’s worth investing your time into.
That’s why we’ve narrowed down four of the most important KPIs you should consider using. Whether you’re a planner or an engineer, each of these four construction KPIs will help you build a clearer picture of your project, improve productivity, and drive site performance.
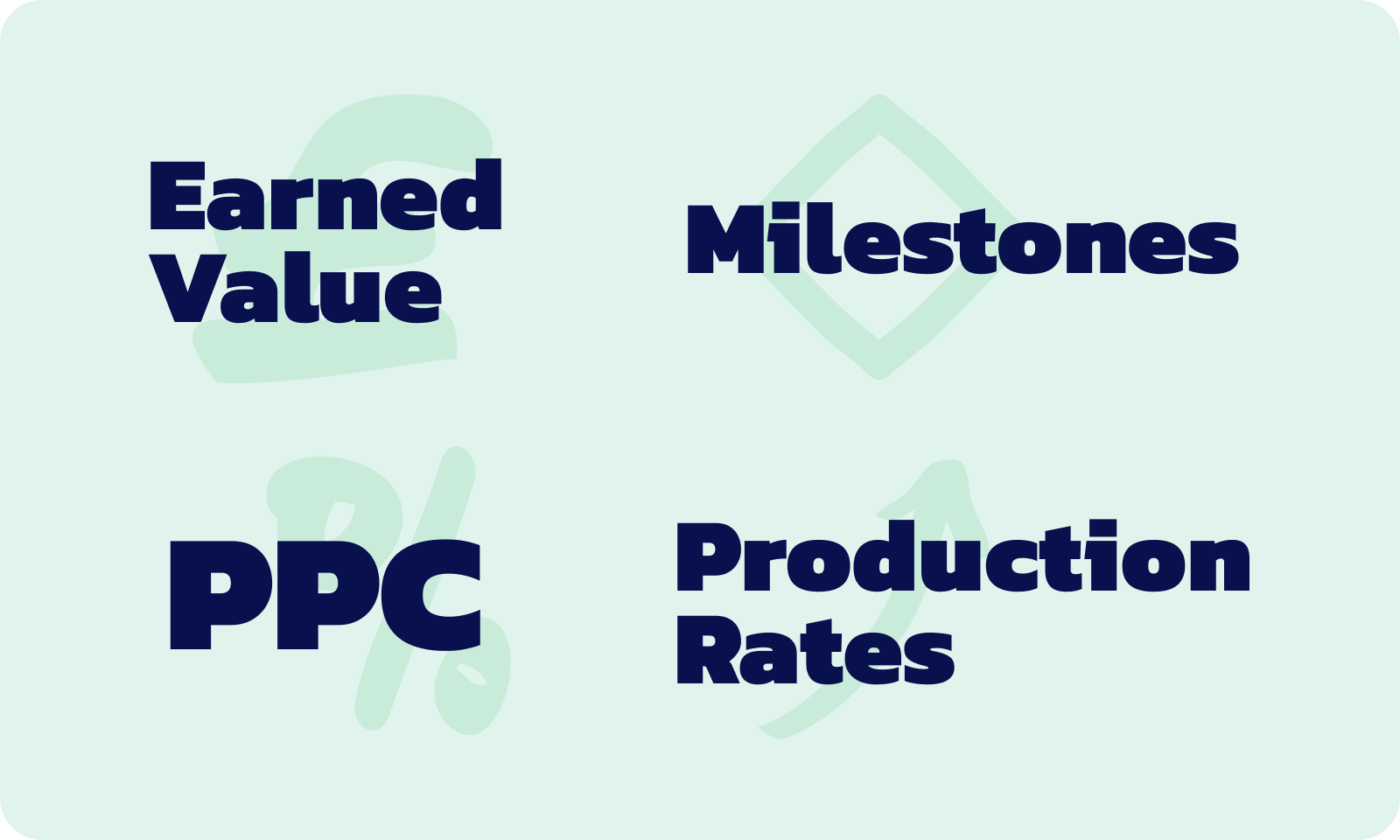
Milestone Tracking
Even if you’re not familiar with the term Milestone, you are almost certainly using them. Milestones are simply a selection of key dates put in place to be tracked over the course of a construction project.
Common Milestones include things like project start and end dates, sectional completion dates, and handover dates.
- Sectional completion dates are the agreed timings for specific tasks or work areas to be completed.
- Handover dates are the agreed timings for an area of work to be passed from one team or trader to another (e.g the date that an electrician will leave a work area and the decorator will start on that area).
Milestone Variance refers to the delay or early completion of a job that has been given a key date. It’s important that you track and monitor variance as this can have a knock-on effect on the rest of the project.
Whilst there are many ways of tracking variance, you will usually find it presented in some form of a spreadsheet dashboard. It’s a relatively simple process as you just need to know the key dates and the number of days that you are behind, or ahead of schedule.
Enjoying this article? You'll love The Ultimate Guide To Construction Reporting.
Earned Value Management
Earned Value Management (EVM) is an analytical tool used in construction to track the progress of a project and compare it against your predicted schedule or budget. You can then use that information to make project forecasts, manage potential risks, and avoid costly delays.
The way it works
Initial project time frames and budgets (as laid out in the Work Breakdown Structure) are used as a baseline to measure performance throughout the project. As the project progresses, you compare the amount of work completed and/or budget that's actually been spent in comparison to your initial plans.
This can then be taken a step further by analysing any variance and investigating the reason for delays and/or additional costs.
Doing this on a regular (often monthly) basis will help you monitor the status of your project. From here you can instigate measures to keep it on track.
For a more detailed breakdown of how to implement EVM you should check out our article on Utilising Earned Value Management In Construction.
Percent Plan Complete (PPC)
Percent Plan Complete (PPC) is used to quantify the success rate of your project so that you measure, and improve site performance.
Traditionally used in lean management systems, this simple, yet effective tool can be easily applied to any project.
The concept works by committing to specific ‘shifts’ at the start of the week - then reviewing how successful those committed shifts were at the end of the week. From this information, you can calculate a percentage of success and quantify your performance.
The routine of committing to and tracking the success or failure of shifts also lends itself to identifying potential issues and carrying out root cause analysis.
Because this is quite a thorough subject, you may find it beneficial to check out our more comprehensive guide on Understanding Percent Plan Complete.
Production Rates
Tracking Production Rate is incredibly useful when you are working on repetitive or linear jobs, such as earthworks or drainage.
This is because these kinds of jobs are less likely to be broken down into smaller tasks. Therefore, you’ll likely find it very difficult to stay on schedule and avoid overspending. That's where production rate can help.
How to calculate production rate in construction
By recording the number of resources used and installed each day, you can estimate the cost of installation.
For example:
You need to lay 5km of waterpipe in 2 weeks (10 working days).
This breaks down to an average of 500m per day that needs installing.
By tracking the meteres installed each day and the cost of the resources used, you can calculate the cost per meter.
Cost of resources used ÷ Quantity of materials installed
By comparing that figure to your budget, you can track whether or not you are overspending on resource.
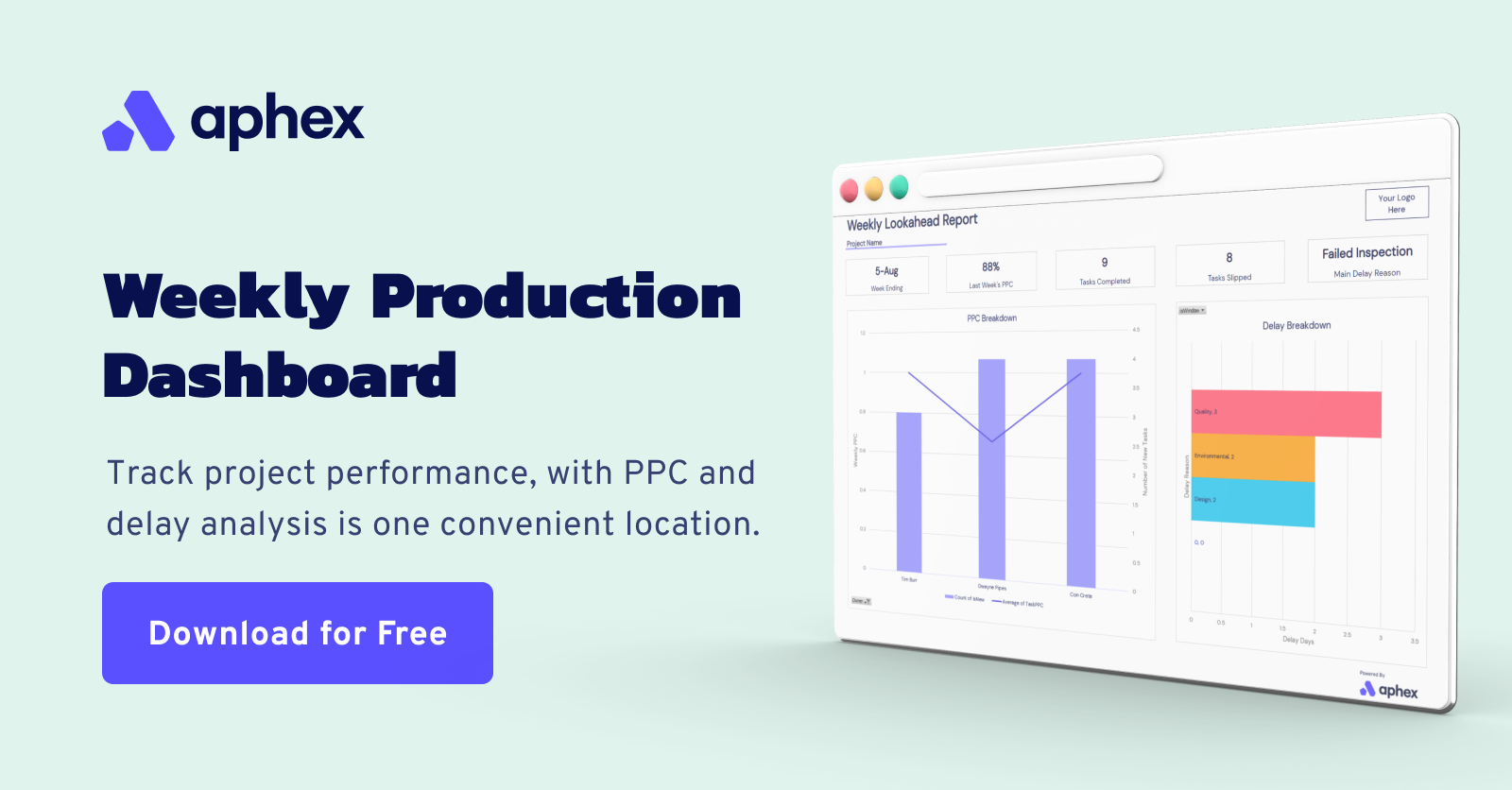
Thanks for reading! If you enjoyed this article and would like to learn more about driving short term performance in construction, check out The Ultimate Guide To Construction Reporting.