If you’ve been around the construction block, you might have heard people talking about things like lean management or the last planner system.
But if you haven’t seen lean management in action, or you want to be able to chime in on the chat next time you’re at the bar with the team, then stick with us.
By the end of this article, you’ll have some idea of what lean construction is, where it came from, and how you’d implement it on your project.
Lean construction management
Lean management offers an alternative approach to traditional construction planning that aims to reduce waste and streamline workflows. In conventional construction management, your project is planned and then constructed. But on a lean project, planning and construction take place at the same time.
Not only that, but the process is carried out in reverse, with delivery teams breaking the project down into smaller, short-term (weekly) plans and working back from there. This approach is often called ‘Pull Planning’ and is part of the last planner system (a topic worthy of its article in the near future).
A quick side note:
You may also come across terms like look-ahead planning and tools like short-term scheduling software being associated with lean construction projects. Whilst these methods and tools can be used in lean management, they’re not exclusive to lean projects.
In our experience, both lean and non-lean projects benefit from look-ahead planning and short-term scheduling software.
The Principles of lean construction
There are six key principles that most projects follow when implementing lean construction management:
1. Respect for people
2. Optimising the whole
3. Removal of waste
4. Focus on process and flow
5. Generation of value
6. Continuous improvement
Because there are so many methods, tools, and ways you can approach lean construction, it helps to have these underlying ‘principles’ to help guide your process and make it clear what you are trying to achieve.
These six principles should always be considered when managing a lean construction project.
1. Respect for people
It’s a pretty simple idea - your team can’t operate at a high level unless the team members respect one another. That’s why team empowerment and respect for people, in particular, sit as one of the core principles in lean management.
Respect is paramount. In order to realise the true value and potential of what you are trying to accomplish, it’s necessary to build your team around the principle of respect.
Do this right, and you’ll find your team is better at sharing ideas and more efficient at solving problems. All things that will lead to more efficient and productive outputs.
2. Optimising the whole
Optimisation isn’t about quick fixes or improving a single section of your work. It’s about improving the whole site over the entire duration of your project.
In traditional construction project management, there tends to be a mentality of “get in, do the work and get out”. Call it a day and move on.
The problem with this is that it’s inefficient. It leads to delays, improved risk and added waste.
Lean encourages delivery teams to give extra thought to what happens before and after the project and individual tasks. Everyone on site should be looking for opportunities to improve.
For more ideas on optimising your project, check out these 5 Actionable steps for a more productive delivery team.
3. Removal of waste
Waste is a huge problem in the construction industry. And with growing concerns over climate change and the use of raw materials, it’s something that needs to be tackled sooner rather than later.
“Construction creates an estimated third of the world’s overall waste, and at least 40% of the world’s carbon dioxide emissions.” - BBC.
Lean construction management encourages teams to think more actively about waste in construction and the impact it has on other teams, stakeholders and the wider environment.
4. Focus on process and flow
Good continuous flow will keep your project on track, which is why lean management encourages you to make it one of your main concerns.
The idea is that through communication and short-term planning, teams can avoid getting in each other’s way, making each other wait, or causing unnecessary delays on site. Lean Construction Institute says this is achieved through “relentless focus on enhanced flow” and by reliably keeping promises and commitments.
The success rate of these commitments are usually tracked and analysed using the Percent Plan Complete (PPC) model. That data can then be used to adjust plans, identify issues, and improve production and ‘flow’.
5. Generation of value
Lean principles take the position that if workers on your project don’t properly understand the value of the project (concerning the owner and the stakeholders), they cannot effectively add value to the parts of the project they are responsible for.
On lean construction projects, the project’s value proposition is usually mapped out and placed around the site so that team members can regularly check themselves and their work against it.
The idea is that people on site should be looking to add value where possible.
6. Continuous improvement
Lean construction management is about continuous improvement, not shortcuts or overnight success. One of the ways it aims to achieve ongoing improvement is by encouraging teams to keep a log of blockers or potential issues that could disrupt productivity on your project.
Those blockers are then analysed by something lean practitioners call the PDCA (Plan, Do, Check, Adjust) cycle so that corrective actions can be taken to get things back on track.
By reporting these blockers, investigating them through root cause analysis, and then taking corrective actions where possible, you can increase project productivity and further support the other principles of lean management.
History of Lean Construction
The ‘lean method’ has been prominent in the construction industry since the late 90s and was initially an adaptation of the famous Toyota Production model. The idea is that by applying the theoretical frameworks used by Toyota to the construction industry, you can reduce waste, over-expenditure, and delays.
Not bad, in theory. But lean is certainly not without its problems. One of the most notable criticisms of this idea is that a complex construction project, where factors change daily, is very different from a production line in a well-organised factory.
You don’t need to have been working in construction long to see why some people might take that point of view.
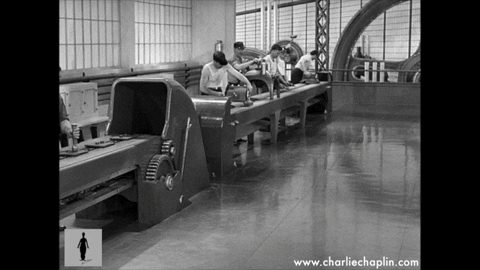
Advantages of lean construction
There are many potential advantages to be had from practising lean construction management. Over the years, there have been several reports of large contractors and site owners seeing reduced waste, fewer risks, and improved profitability.
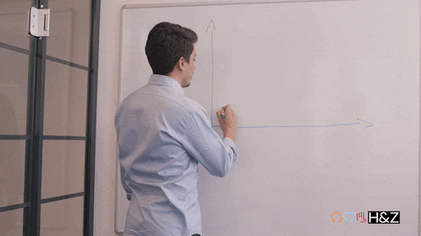
In a 2013 report by McGraw hill construction, they found:
- 77% of projects improved site safety
- 67% reduced waste
- 61% improved profits and reduced costs
Not bad at all.
And on the whole, lean practices could help you improve your project’s performance. But as mentioned previously, lean management is not without its challenges.
Disadvantages of lean construction
One of the main problems with the lean construction method is that it requires everybody involved in the project to be actively committed to carrying out lean practices. And that can be a considerable challenge.
If you fail to get everyone rowing in the same direction, you’re bound to increase in issues, delays, costs, and pretty much everything you’re aiming to reduce.
In A Review On Implementation of Lean Construction Principles, they concluded that “Lean implementation is still a challenge for most practitioners in the construction industry due to varying reasons involved with different levels of personnel involved in various processes”.
The other problem is that if you’re trying to implement lean management on an existing project, you need to account for all the ongoing projects that the new approach could impact.
Not only that, but trying to train teams on the new strategy can take a lot of time.
That’s not to say that you shouldn’t implement lean construction methods halfway through a project, but you should consider these factors before committing to lean management.
How to implement lean construction
Unfortunately, there is no one-size-fits all, cookie-cutter approach to implementing lean construction on your project. This is mainly because every project is unique and requires a tailored approach.
We will say that it helps to keep educating yourself on the different theories and to surround yourself with other people practising lean methodology. It might help to visit another site using lean management or join social groups like this one on LinkedIn.
However you choose to go about it, be prepared to keep learning and adapting as you go forward.