What is Root Cause Analysis?
Root Cause Analysis is a project management tool used to identify underlying issues that cause or contribute towards delays in construction.
Unfortunately, on many jobs, you may not realise the impact of day-to-day problems until it is too late. There is a delay on the project, milestones are moved and a surface-level causation (such as weather) is attributed as the reason why.
However, more often than not there will be a number of contributing factors that could have been prevented before the situation got out of hand.
When carrying out Root Cause Analysis, you question ‘why’ individual tasks and shifts are unsuccessful. Using that information you can then resolve the problem, prevent delays and help keep the project on track.
Why use root cause analysis in construction?
Delays in construction cost both owners and contractors a lot of money. Timelines have to be moved, new resources allocated and it’s ultimately a headache for everyone from the Project Director to the Engineers on site.
The reason this is a flawed approach is that the attributed cause for these costly delays is normally just the tip of the iceberg. By taking a closer look at why your planned tasks are unsuccessful, you can arm yourself with a deeper understanding of what’s really going on, and prevent potential problems.
Let’s say you are an engineer on a project. You’ve put a short term plan in place with specific goals but you have a number of unsuccessful shifts because of faulty equipment. This continues and compounds, ultimately causing a delay on the critical path. The attributed causation is faulty equipment.
Now let’s say that on that same project you carried out root cause analysis, logged every failed task, and investigated the problem further. You may discover that there is insufficient shelter on site and equipment is being left out in the rain, equipment is not being serviced as often as it should be, or the wrong fuel is being used. Armed with this knowledge you can now resolve underlying issues before they amount to something more severe.
In an ideal world, you’d be able to prevent mistakes like this before they ever occur. Unfortunately, the reality is that you just can’t plan for the unforeseen. The next best thing to do is find the root cause of problems and future-proof job as it progresses.
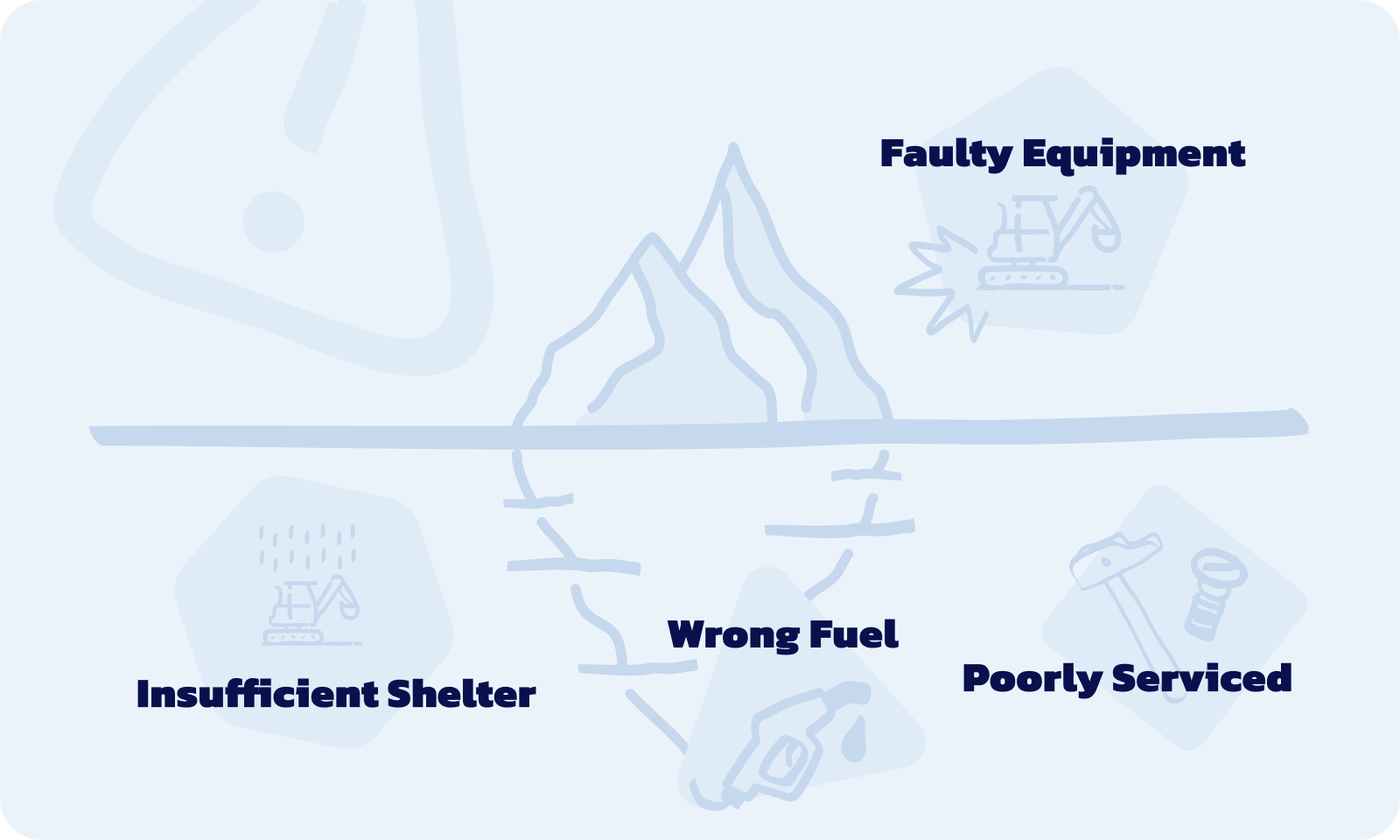
Enjoying this article? You'll love The Ultimate Guide To Construction Reporting.
Getting started
The first step is to start taking note of all your delayed shifts and failed tasks. You can do this using anything from spreadsheets to a notebook. If you are using Aphex to build your short term plans all of your delays and reasons for failure are captured and tracked on your Gantt chart.
One of the more popular ways of tracking task completion is the Percent Plan Complete method. This will help you build an ongoing picture of your task success rate so that you can aim to improve it over time. The important thing to remember is that in order to improve your success rate and reduce potential delays you need to be identifying root causes.
However you decide to track failed tasks, the concept is the same - commit to specific actions and deadlines, then take note whenever those actions aren’t carried out or deadlines are missed. Every time this happens you should be investigating why your plans aren’t successful.
Taking action
Root Cause Analysis will help you identify issues on a project but this information is useless if you don't take action. The next step is to remove the root cause.
Every issue you discover needs to be addressed.
The final thing to note is that root cause analysis is not a one time deal. You should be investigating, analysing, and resolving issues throughout the lifespan of the project and on every failed task or shift.
Do this correctly and you will help save the project from costly delays and yourself from complicated problems and headaches.
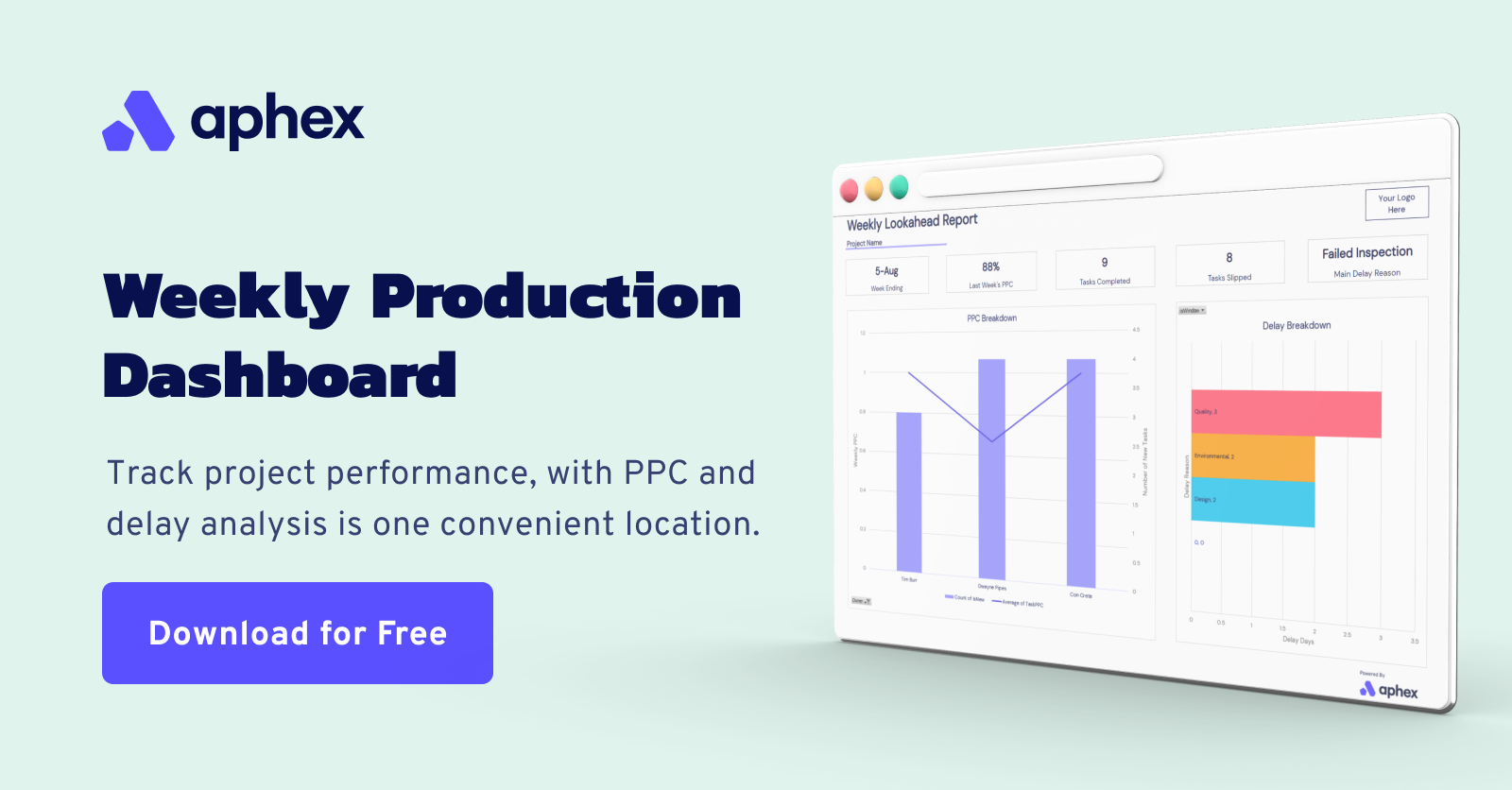
Thanks for reading! If you enjoyed this article and would like to learn more about driving short term performance in construction, check out The Ultimate Guide To Construction Reporting.